The wastewater treatment plant in Lüneburg in the state of Lower Saxony Germany, was designed to meet the needs of around 325,000 inhabitants. It features numerous treatment tanks up to 7m deep, where the air for the biological treatment processes is delivered via a control valve. Until recently, the compressed air for this aeration was generated by four conventional turbo blowers, each with a power output of 200 kW. However, the operator was looking for a new solution that would enable more wide-ranging, direct and dynamic control of compressed air production than the existing control system. They also wanted the benefits of a constant air supply that would not be affected by adverse weather conditions. Because the air flow and power consumption data are precisely tracked and logged, the benefits of the newly-installed rotary screw compressor quickly became apparent. The KAESER’s HBS series blower was subjected to a maximum usage test during the course of a one-year trial at the Lüneburg treatment plant. Because the existing control technology was set up for turbo blowers with adjustable guide vanes, the software needed to be adapted for a speed-controlled rotary screw blower. When the blower reaches a certain speed threshold, a turbo is switched on or off as needed to avoid inefficient overlapping. A direct performance comparison of the two machines shows us that, in almost 24-hour operation, including 12 hours running alone, the single blower matches the performance of a turbo delivering 4000 – 9000 m³/h. In terms of power consumption, the rotary screw blower, running in conjunction with the turbos, emphatically demonstrated that savings of around 250,000 kWh/year could be made, representing around 10–15% of the current annual total.
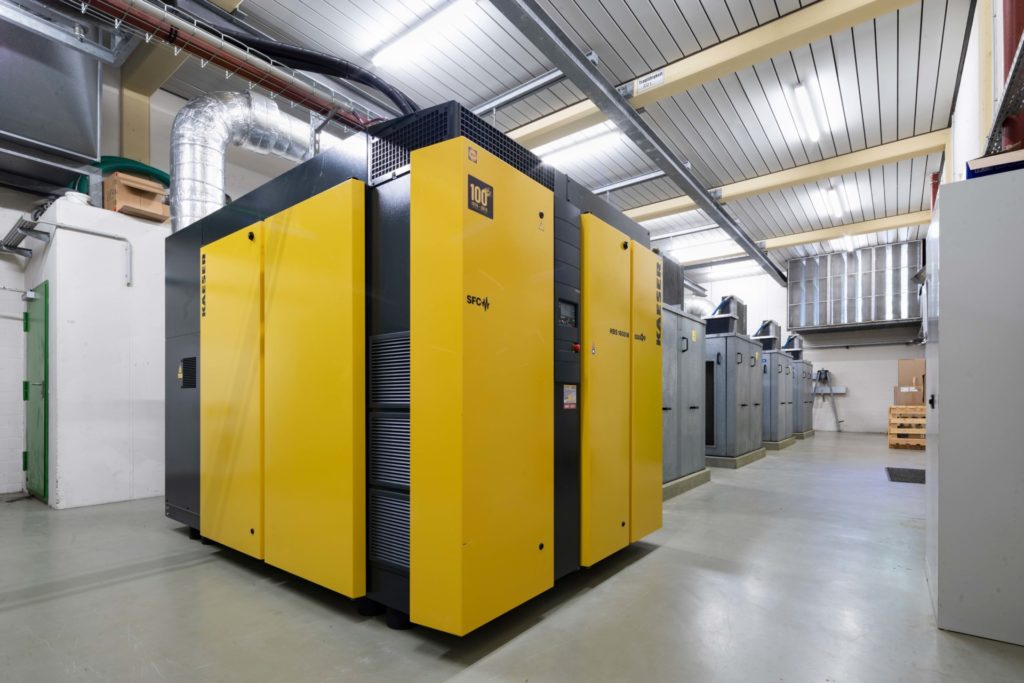
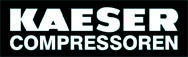
Rotary screw blower in perfect harmony with turbo blowers
Energy efficiency is becoming an increasingly important factor in wastewater treatment.
Delen:
Facebook
Twitter
LinkedIn
WhatsApp
Contactinformatie
Stuur ons een bericht
- 7621 HB,
- Borne,
- Netherlands